Testing benches with differential technology for the new VW APP550 engines
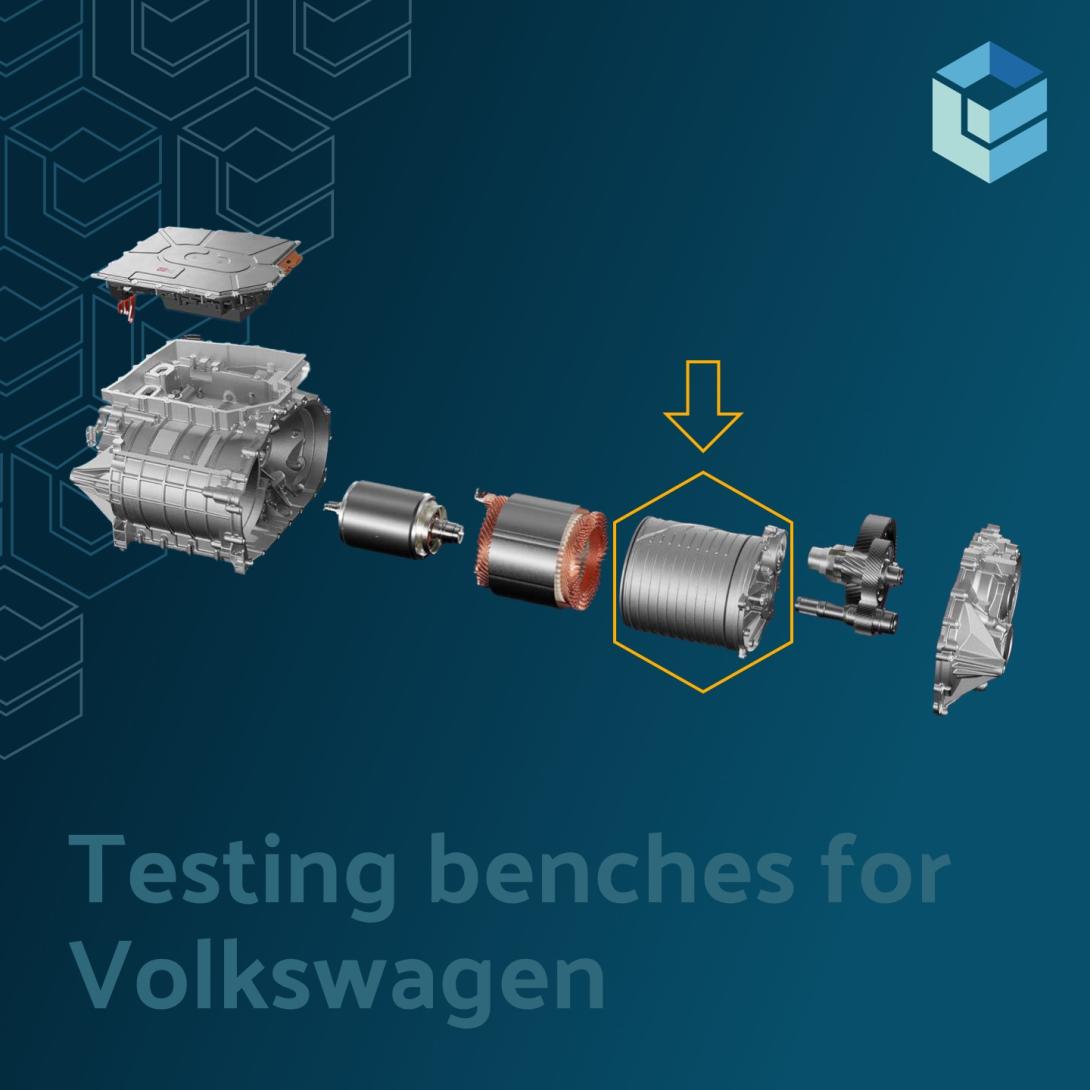
ECB Ltd has constructed testing benches with differential technology for the new engines of Volkswagen.
In 2023, Volkswagen introduced the new electric engine, the APP550, for cars utilizing the MEB platform. Redesigned from scratch, it promises enhanced performance and improved efficiency. The engine is manufactured at the Kassel factory and makes its debut on the ID.7; it delivers a maximum power of 286 hp and a torque of 550 Nm, the highest ever made available on current models, which previously capped at 203 hp and 310 Nm.
The APP550 achieves this high torque thanks to an improved stator, featuring more windings, a larger wire section, and thinner casings to optimize material usage.
The engine is also innovative due to its different layout, with all components integrated into a single module: it includes the actual drive unit, the rotor, the stator, and the cooling jacket highlighted in the following image.
The entire thermal management of the engine has been redesigned, and employing a variable-displacement electric oil pump and the transmission components themselves to transfer heat, allows for a reduction in energy consumption for the thermal management of the powertrain. For the stator, a separate water-cooled heat sink has been provided to dissipate the high heat generated by the windings when maximum performance is required.
ECB Ltd has constructed testing benches with differential technology for the new engines of Volkswagen
The supplier of the heat exchanger for cooling the stator of this new electric motor has turned to ECB for the construction of the necessary testing benches for the new department, which can produce over 700,000 units per year. The heat exchanger surrounding the stator is a thin-walled aluminum die-casting through which the coolant flows, and within which the stator windings are housed. It is therefore essential that after the internal turning process, the absolute absence of cracks or porosity is guaranteed, as these could lead to the entry of liquid towards the internal stator and rotor.
For the initial pre-production supplies, ECB initially constructed the second-level control bench, which allows testing the seal of the components both dry and by immersing them in a heated water tank to emphasize leaks through the expansion of the die-casting and identify their location by locating the point of exit of air bubbles.
Simultaneously, two two-station independent testing machines were designed and built, totaling four stations, which will be an integral part of the robotic processing, washing, finishing, and testing island for the mass production of this essential component for these new electric motors.
Each machine has been designed to allow manual loading by an operator, in addition to automated loading managed by an anthropomorphic robot, which will be the standard in mass production. For this purpose, each station has been conceived as completely independent, including safety devices, allowing the loading/unloading of one station while the others continue to operate.
Differential testing bench modules: high-performance "tailored" solutions
New differential leak test modules have been employed on the testing stations for the robotic island, offering a range of particularly interesting features for battery applications:
- Modular architecture: Module connections are minimized, and the ECB software can handle a variable number of modules in a completely independent and asynchronous manner, virtually without limits.
- High resolution even at high test pressures: Standard pressure ranges extend up to 12 bar, but in special configurations, it can go up to 30 bar, always ensuring a resolution of 0.01 mbar, impossible to achieve with normal relative pressure transducers.
- Electronic pressure regulation: The module automatically and autonomously manages the regulation of the test pressure.
- Self-test circuit with a calibrated leak: The valve group integrates the solenoid valve and the outlet fittings for the connection of a calibrated reference leak, allowing the periodic execution of self-test cycles.
- Very competitive cost: Our modular architecture allows for increasing savings as the number of parallel test stations grows, compared to the use of stand-alone single-channel leakage testers.
Would you like to receive further information about an automatic leak test station? Contact us.