Test Systems for Automotive Brushless Motors and Pumps
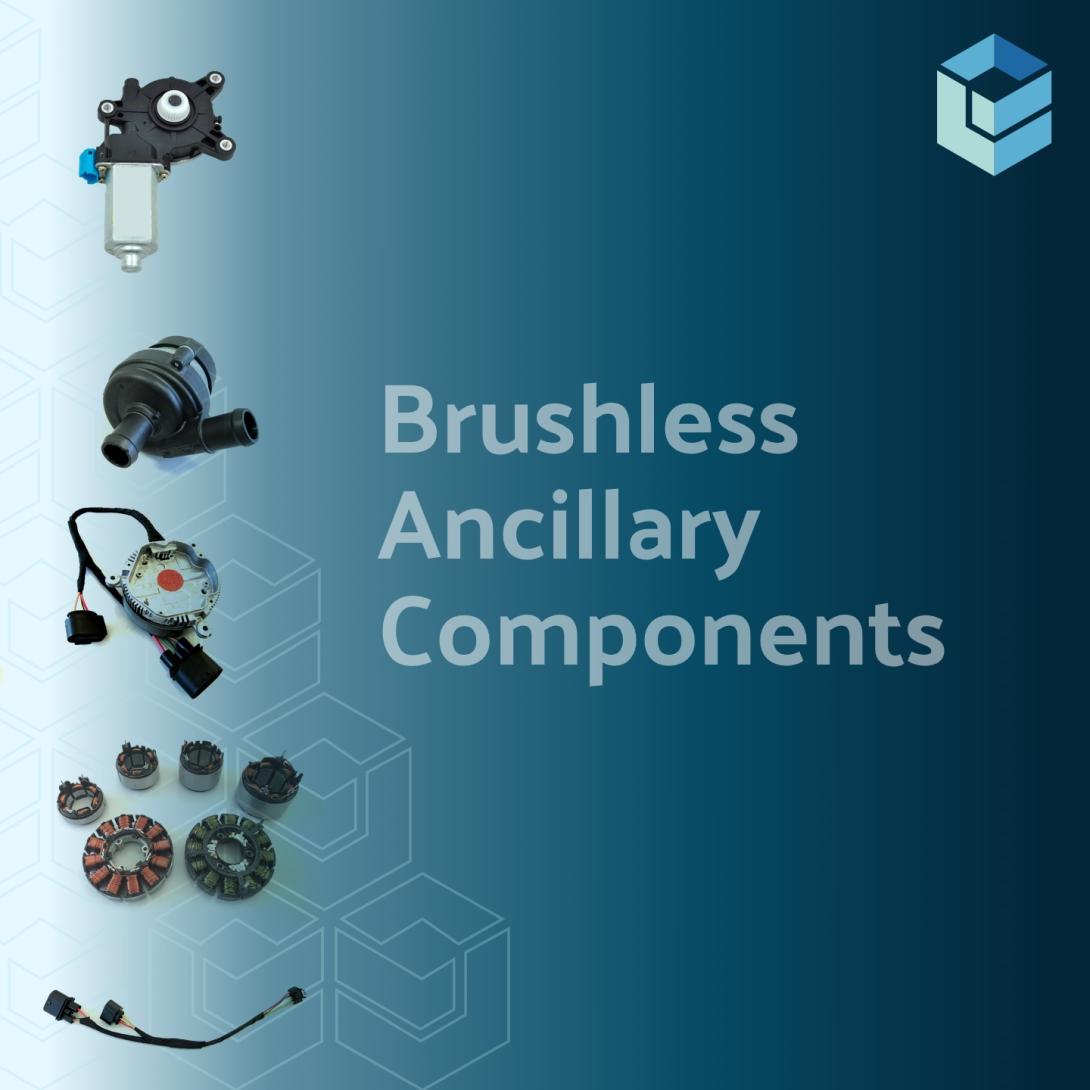
In this article:
- Stator Winding Testing
- Test Systems for Wiring and Semi-Assemblies
- Functional Final Testing of Complete Motors and Pumps
- ECB Expertise at the Service of Manufacturers of Stators, Motors, and Brushless Pumps
In recent years, the increasing demands for performance optimization and consumption reduction across all vehicle classes, along with the development of full electric models, have also led to innovations in components not directly involved in propulsion generation, the so-called auxiliary components.
This has resulted in a gradual replacement of components traditionally driven directly by the engine (or via belts) or operated by traditional DC motors, with new versions featuring brushless motors with digital control:
- Variable flow engine oil pumps
- Primary and auxiliary cooling pumps
- Air conditioning compressors
- Cooling fans for radiators and cabin air conditioning
- Window lift gearmotors
These new components ensure:
- Greater efficiency
- Continuous speed control
- State monitoring
Concurrently, the introduction of electronics into components that were previously purely mechanical or employed traditional DC motors has led to new requirements in the field of test systems, especially for products that require digital control to function.
Many motors and pumps used in vehicle lubrication and thermal management allow continuous control of speed and continuous monitoring of status to signal to the engine control unit or body controller whether the operation is regular or if there are anomalies.
This is achieved through a PWM modulated signal or via communication buses, LIN or CAN; hence, the test system must manage such signals by simulating onboard vehicle protocols.
ECB provider of stator test systems, insulation testing, BEMF tests, leak and functional test systems.
For manufacturers of brushless motors and pumps, in recent years we have developed laboratory test benches and test systems for large automated lines.
Stator Winding Testing
For the testing of stators, it is generally provided:
- Measurement of phase resistance and inductance, to detect defects in the copper wire or in the welding process.
- DC insulation and/or AC dielectric strength tests, to ensure proper insulation of the windings relative to the laminations that make up the magnetic circuit.
- Surge tests to detect more hidden defects such as short circuits between turns caused by abrasion of the enamel insulation of the copper wire during the winding process on the pole expansions.
Test Systems for Wiring and Semi-Assemblies
For the testing of wiring and stator/rotor semi-assemblies still without electronics, it is generally provided:
- Continuity tests to verify that the cable molding process has not damaged the welds between cables and terminals.
- DC insulation and/or AC dielectric strength tests to ensure proper mutual insulation between different terminals and between terminals and the metal body of the motor or pump.
- BEMF tests to verify the absence of construction defects in the rotor (insufficient magnetization of the magnets, misalignments) and of magnetic coupling with the stator.
Functional Final Testing of Complete Motors and Pumps
For the functional final testing of motors and pumps, very detailed testing specifications are generally provided, to ensure coverage of all functionalities and possible causes of defects.
In this phase of the production process, it is possible to proceed with:
- Leak tests to verify that any sealed sections do not have defects that would allow potential ingress of moisture or water towards the electronics or loss of fluids from the cooling circuit.
- Sleep and stand-by current tests to ensure that the component does not cause battery discharge due to an excessively high rest current.
- Functional tests, under variable load conditions, to verify that expected performance is met even at full load.
- Product customization through electronic board parameterization.
ECB Expertise at the Service of Manufacturers of Stators, Motors, and Brushless Pumps
Years of experience allow our company to guarantee for every test system we supply:
- Selection of the most suitable components: for measurement applications like those required in this sector, the accurate selection of each component is crucial, as even a suboptimal cable or connector could degrade the precision characteristics of the entire system.
- Development of dedicated hardware: in many cases, we develop special boards to integrate the control and measurement front-end, optimized for the specific application.
- Co-design of the test station with the client and the possible supplier of the production line: we also provide assistance for the correct design of the contact heads, piece supports, connections on board the machine, ensuring that the technical solutions are optimal from the connection tool to the tested piece to our testing equipment.
- Customization of control software: every client has different needs, implementing dedicated functionalities is our standard.
Would you like to receive more information about a test system? Contact us.